Jak výběr vstřikovaného materiálu ovlivňuje cyklus
6.375.000,-Kč (slovy šestmiliónůtřistasedumdesátpěttisíc kourun českých) úspora a stačilo tak málo.
Manažerské shrnutí:
Celkové zkrácení cyklu v reálné praxi: 15 vteřin na cyklus
finanční úspora: 5 let pouze na provozu znamená úsporu 1.875.000,-Kč
Celková úspora: za 5 let na cca 6 375 000 Kč (detaily viz článek)
Kontakt: na konci článku
Zadání
Při zachování kvality zkrátit cyklový čas výroby a vyhodnotit finanční dopad. 2K forma, materiály PP a TPV. Plnění elastomeru je zajištěno pomocí jednoho středového vtoku. Při tečení do koncové části dílu musí materiál překonat vzdálenost 425 mm s průměrnou tloušťkou stěny 1,3 mm.
Pro běžné termoplasty jsou tyto podmínky délky tečení nepřekonatelné, ale pro termoplastické elastomery, vykazující se vysokou tekutostí, dosažitelné.
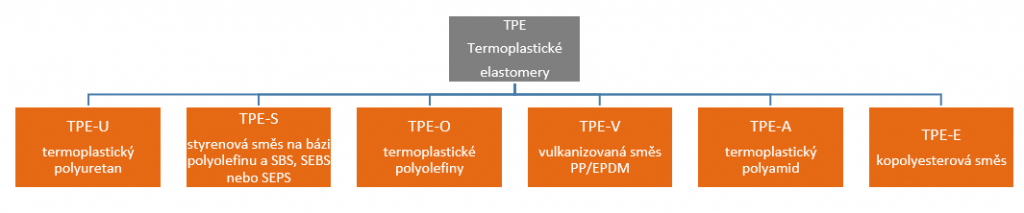
Trocha teorie
Termoplastické elastomery (TPE) jsou moderní polymerní materiály, které mají vlastnosti elastomerů a zpracovávají se jako termoplasty. Na trhu je k dostání mnoho odlišných typů termoplastických elastomerů (TPE) se specifickými vlastnostmi.
Velmi často se ve symbolické zkratce vypouští písmeno „E”, následně se používá označení TPU, TPS, TPO, TPV, TPA, a TPE.
Jednotlivé typy materiálů se liší dosažitelnou tvrdostí, elasticitou, teplotním intervalem použitelnosti, chemickou odolností a hustotou. U 2K vstřikování je navíc velmi důležitá soudržnost se základním materiálem.
Na díly z termoplastických elastomerů se kladou stejné nároky jako na díly z termoplastů. Z ekonomického hlediska (především délky cyklu vstřikování) je snaha zlevnit vyrobený díl a jít s technologií na samou hranici výroby kvalitních dílů.
Původní stav
Původní výrobní cyklus měl 55 s, z toho plnění dutiny formy probíhalo 3 s, strojní časy na vyjmutí dílu a uzavření, otevření a otočení formy byly 15 s. Naší snahou bylo celý výrobní cyklus co nejvíce zkrátit, protože 1 uspořená sekunda na výrobním cyklu, znamená roční finanční benefit 75 000 Kč. Při plánované produkci 5 let už začíná být i jedna výrobní sekunda ekonomicky zajímavá.
Zkracování cyklu je v projektech velmi populární téma, ale v žádném případě nesmí zvýšit zmetkovitost výroby. Ideální je zařadit optimalizaci výrobních parametrů do vývojové fáze procesu, ale minimálně v 99,9 % realizovaných projektů chybně nastává optimalizace až ve fázi výroby. V běžící výrobě je bohužel možné měnit a upravovat pouze menší množství parametrů, kterými lze cyklus optimalizovat bez snížení kvality dílu, než ve fázi vývoje!
Doba tečení termoplastického elastomeru TPV dutinou formy byla ve výrobě 3 s, v simulaci byl vypočten tlak taveniny na vstupu do formy 105 MPa. Předpokládaná doba plnění takového dílu je 1 s. Při zvýšené rychlosti plnění vychází tlak na vstupu do formy 115 MPa. Ve výrobní zkoušce, se nepodařilo času 1 s dosáhnout ze dvou důvodů. První příčinou je příliš dlouhý a málo dimenzovaný systém horkých vtoků, ve kterých dochází k velkým tlakovým ztrátám. Druhá příčina vychází z té první. Stroj potřeboval příliš velký tlak na vstřikování, kterého nebyl schopen dosáhnout. Vstřikování probíhalo s maximálním omezujícím tlakem minimálně 2,5 s. Při takto nastaveném procesu plnění docházelo k nestabilitě polštáře i hmotnosti dílu.
Vzhledem ke konstrukci formy a použitému lisu – tedy věcem, které v běžícím procesu výroby nelze změnit – je možno upravovat pouze technologické parametry procesu a zkusit změnit materiál. Jednou z možností je technologicky zvýšit tekutost materiálu, což u zvoleného TPV má za následek jen malé změny ve vstřikovacím tlaku.
Navrhované řešení:
Vzhledem k aplikačním požadavkům byl navržen alternativní termoplastický materiál na bázi TPS THERMOLAST® K TC7WEZ. Při vstřikování TPS elastomeru se výrazně snížil maximální tlak na vstupu do formy na 51 MPa. Doporučená doba plnění formy za 1 s je bez problémů dosažitelná a výroba zůstává stabilní. Při této rychlosti tečení je nutné zajistit kvalitní odvzdušnění, u TPV i TPS je vhodný SGD ventil do vyhazovače na konci dílu, či ventil Ecovent s malým přetokem. Při plnění TPS materiálem dochází k úspoře 2 sekundy na době tečení plastu dutinou formy.
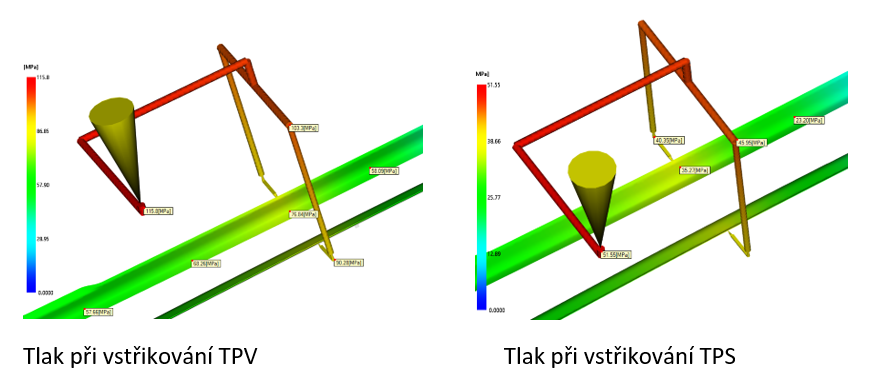
Další úspory
Zaměříme-li se detailně na hledání možnosti úspory, tak můžeme porovnat i hustotu použitého TPV 0,950 g/cm3 a nového TPS 0,930 g/cm3. I tento nepatrný rozdíl v hustotě znamená v ročním součtu úsporu cca 166 kg materiálu (cca 13 000 Kč/rok).
Další úspory můžeme hledat v nejdelší části výrobního cyklu. Zaměříme se na dobu chlazení. Provedli jsme podrobnou analýzu celé formy ve 3D, která ukazuje tepelné toky skrz celou formu i díl. Zkušebně byly provedeny výpočty pro kratší doby chlazení a nižší teplotu temperačního média. Výpočty s nižší teplotou formy nevykazovaly výrazný vliv na rychlost tuhnutí vnitřní části TP dílu a neumožnily zkrácení doby chlazení. Zároveň přinesly problémy s plněním a deformacemi nosného polypropylenového dílu.
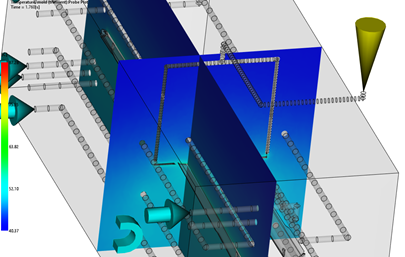
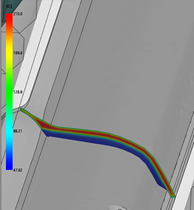
Možnost zkrácení doby chlazení závisí na schopnosti materiálu přejít do tuhého stavu a během dochlazení na vzduchu vykonat deformace v požadovaných tolerancích. Po detailním rozboru chlazení formy i dílu, simulace našla v době chlazení možnost zkrácení cyklu o 7 sekund. V reálných testech bez problémů fungovalo zkrácení o 5 s, zkrácení doby chlazení o 7 sekund je na hranici výrobních tolerancí a hrozí neshodné díly.
Výsledek
Celkové zkrácení cyklu v reálné praxi: 15 vteřin na cyklus
finanční úspora z cyklu: 5 let pouze na provozu znamená úsporu 1.875.000,-Kč
Celková úspora: za 5 let na cca 6 375 000 Kč
Cena MF analýzy: zanedbatelná
V případě použití alternativního materiálu na bázi TPS (THERMOLAST® K TC7WEZ) s 1,6 x vyšší tepelnou vodivostí vychází úspora na cyklu ještě výrazněji. Při stejném zatuhnutí a deformaci v požadované toleranci vyšlo zkrácení cyklu o 15 sekund. Rozdíl v době chlazení obou optimalizovaných cyklů různých materiálů je 10 sekund a v době plnění 2 sekundy.
Použijeme-li výsledky provedené simulační analýzy pro TPV materiál – tedy zkrátíme dobu cyklu výroby (přesněji dobu chlazení) – získáme za dobu 5 – ti letého projektu úsporu ve výši 1 875 000 Kč.
Vyčíslení úspory u TPS materiálu je vzhledem k nezveřejnění přesných obchodních cen složitější. Maximální možná úspora (zahrnuje zkrácení cyklu při použití TPS materiálu s lepší tekutostí a lepší tepelnou vodivostí), oproti původnímu nastavení technologie výroby, vychází za 5 let na cca 6 375 000 Kč. Tuto částku ale musíme ponížit o rozdíl v ceně materiálů.