Online sledování forem a střihacích i tvářecích nástrojů
Motivační otázky: Víte, co se aktuálně děje s Vaším nástrojem či formou? Máte kompletní podklady na jednom místě k použití? Jaké jsou aktuální funkční technologické parametry?
Jaký je počet zdvihů? Kontrola preventivní údržby? Jak řešíte neshodné výrobky z nástroje? Lze toto řešení urychlit? Jak Vaše firma řeší zachování znalostní databáze svých pracovníků a jejich zastupitelnost? Elektronický provozní deník? Na tyto a mnohé další otázky přináší odpověď patentovaný systém firmy MachineLOG IT, který obsahuje kompletní znalostní databázi k problematice provozu a údržby pro formy na plasty a lehké kovy, střihací a tvářecí nástroje. Abychom tento systém automatické archivace znalostí mohli dobře popsat, udělejme si nejdříve malou exkurzi do historie výroby.
Úvod
Požadavky na výrobu na přelomu tisíciletí se vyvíjely tímto způsobem:
70. léta: hromadná výroba
80. léta: kvalita výrobků
90. léta: kvalita výrobních procesů
rok 2 000: RYCHLOST
Systém výroby obecně se vyvíjel směrem od jednoduché ruční výroby v podstatě „na koleně“ přes hromadnou (sériovou) výrobu, kterou zavedl například Tomáš Baťa a Henry
Ford. Systém sériové výroby byl natolik silnou konkurenční výhodou, že v podstatě vytlačil jiné, neproduktivní formy výroby. Známé a popsané jsou komentáře ševců, kteří nevěřili tomu, že by je takto koncipovaný systém (předdefinované velikosti bot) mohl vytlačit z trhu. Jejich nepřizpůsobivost zapříčinila jejich ekonomickou porážku a dominanci hromadné výroby. V 80. letech pak byla konkurenční výhoda definována kvalitou výrobku. Firmy se nacházely ve fázi, kdy dokázaly vyrábět produkty hromadně a jejich odlišení se začalo definovat kvalitou. Tuto dobu si ještě mnoho lidí u nás pamatuje jako dobu, kdy naše podniky začaly ztrácet dech, právě z důvodů kvality výroby. Cílem tehdejší doby v Československu bylo „dohnat a předehnat“. Toto známé moto postupně v lidové slovesnosti získalo dodatek „…nebo alespoň neztratit z dohledu“. Frustrace našich techniků té doby byla enormní.
V následné fázi období devadesátých let, kdy primární slovo v inovacích měla kvalita výrobních procesů, se naší republice povedlo, za cenu obrovských investic, stáhnout náskok vyspělejších zemí a dosáhnout konkurenceschopnosti i kvalitou výrobku. Zahraničí se ale mezitím posunulo do další kvalitativní fáze a hlavní inovace probíhaly v oblasti kvality výrobního procesu. Kvalita výrobku tedy byla požadována automaticky a byla determinována kvalitou celého výrobního procesu.
I na tuto změnu dokázaly naše firmy reagovat, ale opět se zpožděním. Dávno pryč byla doba, kdy české firmy, mimo jiné prezentované firmou Baťa, udávaly směr technického a
technologického vývoje.
V období po roce 2000 se primární úsilí modernizace podniků napřelo směrem na rychlost. I na tuto fázi dokázaly naše podniky zareagovat, a to i přes nepříznivé možnosti odpisů investic v naší republice.
Po roce 2 000 se ukázalo, že výrobní možnosti jsou po celém světě relativně vyrovnané a hlavním rozlišovacím prvkem, který odlišuje a vyzdvihuje kvalitní firmy nad průměr, je know-how jejich pracovníků.
V této době přišel na trh systém MachineLOG IT, který se snaží podpořit, zefektivnit a zautomatizovat proces archivace znalostí zkušených pracovníků pro firmu. Největší problém dnešních podniků je předávání znalostí ze starší generace na nově nastupující. Kam až může tento problém vést ukázaly minulé roky ve Španělsku, kde nezaměstnanost dosáhla 27 % a nezaměstnanost mezi mladými do 25ti let přesáhla 56 %. Ztráta znalostí a zkušeností dále podlamovala španělskou ekonomiku a start prorůstových opatření narážel na problém know-how. Španělské firmy měly kvalitní vybavení, měly dokonce i zakázky, ale jejich konkurenceschopnost ve výrobě klesala, přičemž dolů je tlačil nedostatek znalostí a zkušeností s výrobou.
MachineLOG IT je postaven tak, aby maximálně zjednodušil dva největší problémy znalostních databází dneška, a to zápis informací do systému a jejich vyvolávání a čtení. V dnešní době není problém nasadit systém znalostní databáze, ale problém je její naplnění a hlavně vyvolání relevantní informace tehdy, kdy je tato informace potřeba. Dnešním firmám schází systematizované předávání zkušeností, a to i z toho důvodu, že neexistují kompletní podklady pro interní školení řešených problémů tak, aby se tato znalost rozšířila mezi co nejvíce technických pracovníků a tím se zlepšila celková konkurenceschopnost firmy. Technické vzdělávání pracovníků probíhá nahodilým ostrůvkovým procesem ve stylu posezení u kávy a větami typu „…Pepa prý řešil nějaký problém, slyšel jsi o tom?“ Toto je další oblast, kterou se systém MachineLOG snaží změnit. Při důsledném používání systému MachineLOG IT, je možné dělat pravidelné výstupy pro systematické technické školení interních pracovníků s kompletním popisem chyby, její obrazovou dokumentací a následným zdokumentovaným řešením. Takto popsaná znalostní databáze nejen urychluje řešení dalších problémů ve výrobě, ale také je vynikajícím základem pro sdílení znalostí napříč firmou a rychlé ustavení nových firemních standardů. Díky kvalitním podkladům lze pružně reagovat na opakující se chyby a systémově jim předcházet pomocí interních předpisů a vzdělávání pracovníků. Cílem je převést maximum možných řešení do oblasti prevence, nikoliv udržovat řešení v oblasti reaktivních systémů. Bohužel je jasné, že převést 100 % řešení z reaktivní do preventivní či dokonce prediktivní oblasti není technicky možné, ale výsledek limitně se blížící preventivní oblasti je rozhodně cíl, který dokáže uspořit firmám nemalé náklady.
Použití nástrojů – jak a kdy?
Nasazení, údržba, prevence a kvalita výroby
Zásadní otázka sledování nástrojů se dá zjednodušit na boj mezi manažery projektů a výkonnými pracovníky. Zatímco řídicí pracovníci by chtěli maximum informací pokud možno v reálném čase, výkonní pracovníci jsou časově zaneprázdněni samotnou výrobou a přepisování informací do systému je nijak zvlášť nezajímá, ba naopak je zdržuje od jejich hlavní práce.
Kde se forma nachází a co se s ní aktuálně děje?
• Jak je forma uskladněna?
• Jak je forma provozována?
• Jakou kvality mají aktuální výlisky při stávajících parametrech?
• V jaké fázi je preventivní údržba formy? Už je demontována / vyčištěna /
navařena / složena?
A navíc: JAK zjistit tyto informace bez zdržování výrobních pracovníků? Výroba má vyrábět, nikoliv zadávat informace a hrát si na písařku. Další problémy mohou nastat a nastávají při transferu forem mezi závody. Existuje někde kompletní databáze s historií formy? Rychlé odpovědi na tyto otázky dokážou uspořit nemalé finanční prostředky.
A co transfer?
Při předání formy od jiného závodu je možné předat kompletní databázi o provozu formy jako součást podpory. Díky tomu, že systém je šablonován a překládán do více jazyků, je jednoduché podpořit zahraniční pobočky v jejich mateřském jazyce. Součástí transferu tedy bude kompletní 2D a 3D dokumentace, funkční parametry, popsané problémy a jejich řešení včetně fotodokumentace stavu. Součástí je i kontakt na nástrojárnu a dodavatele dílů forem včetně rozpisky náhradních dílů. Urychlení transferu a možnosti vyžádat si podporu je tedy výrazně vyšší než u standardního transferu pomocí papírové dokumentace.
Jak systém pracuje?
Základem systému je šifrovaná databáze s odstupňovanými přístupovými právy, která umožňuje jednoduše sledovat pohyb nástrojů a jejich aktuální stav. Pro využití systému stačí chytrý telefon nebo tablet s datovým připojením. Do systému lze rychle vkládat informace včetně obrazové dokumentace stavu nástroje a grafických poznámek.
Každá forma je vybavena unikátním QR kódem, který umožňuje vstup do šifrované databáze. Výrobní pracovník tedy sejme QR kód pomocí chytrého telefonu s nahranou aplikací MachineLOG IT s nadstavbou „formy“. Tato aplikace převede číselný kód na adresu do šifrované databáze a dle přístupových práv povolí pracovníkovi provést potřebné úkony.
Je samozřejmé, že jiné pravomoci na prohlížení a zadávání informací bude mít vedoucí projektu a zcela jiné obsluha lisu. Toto víceúrovňové řízení se pozitivně odráží na rychlosti a jednoduchosti zadávání dat do systému. Pracovník, který nebude zatěžován nadbytečnou administrativou, bude tyto informace zadávat ochotněji, než osoba, která musí dublovat zápisy na papír a pak je přepisovat do počítače. Další výhodou je minimalizace rizika chyb při zadávání informací. Toto riziko se jakýmkoliv přepisováním zvyšuje. Mnoho proměnných lze sledovat na principu Ano/Ne – tedy pouhým kliknutím na ikonu, s eventuálním doplněním informací buď ručně (napsáním), nebo pomocí e-fotografie.
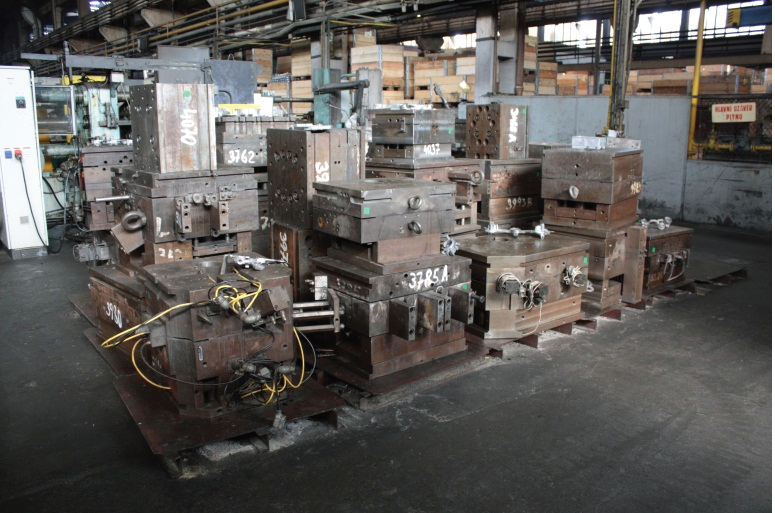
Pokračování příště.
www.jansvoboda.cz
www.machinelogit.com